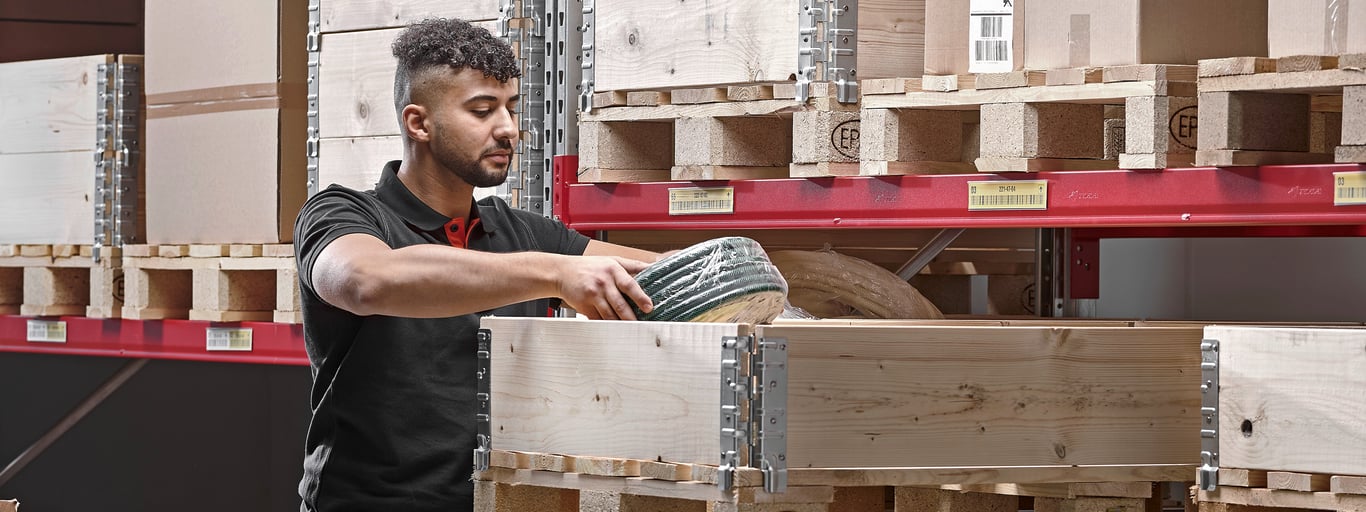
Tips for more efficient warehouse logistics
Inventory, management and logistics
To effectively plan the purchase of goods, consider implementing a digital inventory control system. In order to satisfy the customers' wishes, you need to have the right products for the lowest possible cost at the same times as they are requested. Optimize inventory to increase turnover and prevent costly overstock.
When goods are loaded and unloaded frequently, a robust stock management system is essential for accurate stock tracking and efficient warehouse logistics. Smooth administration and systematic storage are of the utmost importance. The interior of the warehouse should be planned by using the knowledge you have from the logistical flow of goods. Our expert tips can help create optimal warehouse conditions.
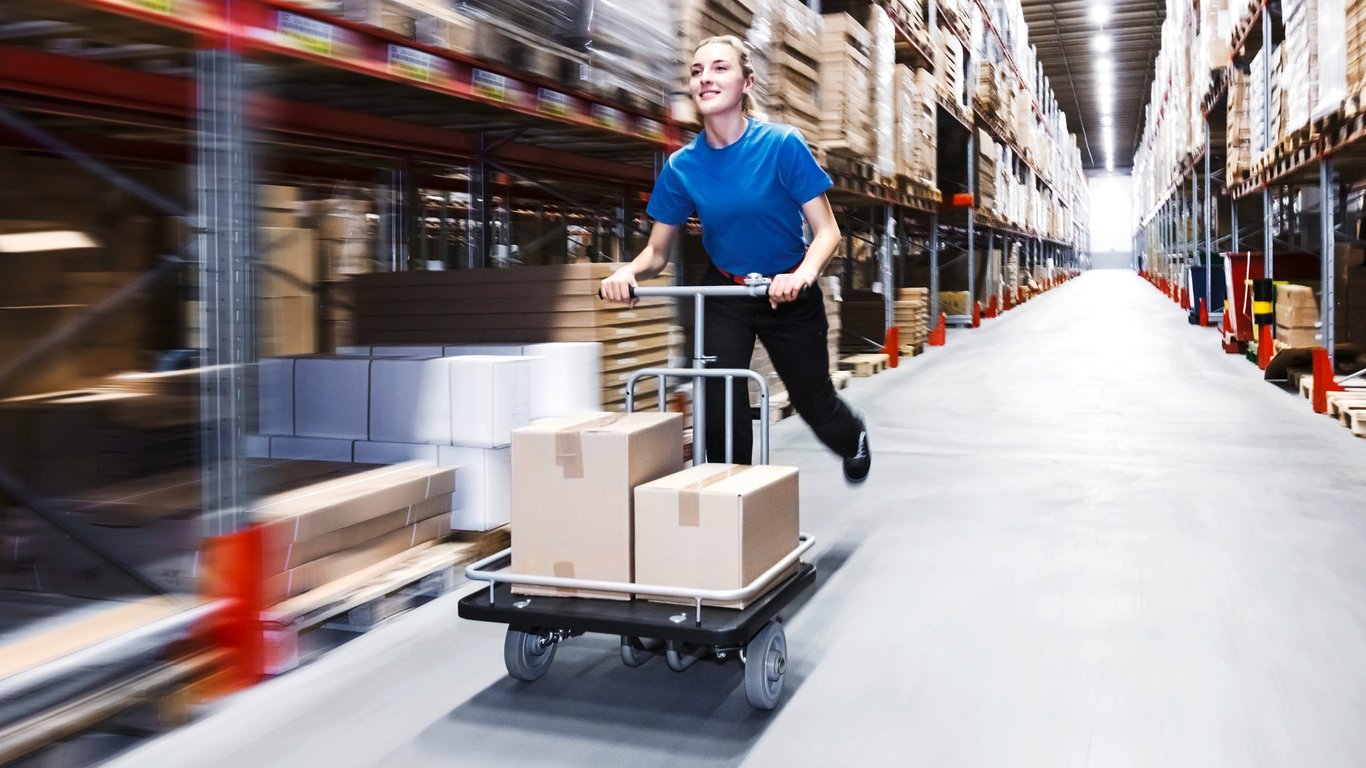
Have the best sellers close at hand
Efficient placement of high (and low) frequency goods is crucial for optimizing warehouse operations. Strategic accessibility to your top-selling products minimizes unnecessary time moving around the warehouse, enhancing productivity. Similar to organizing a kitchen, thoughtful planning can elevate the efficiency of storage and logistics systems. A place for everything and everything in its place – nowhere is this more applicable than in a warehouse.
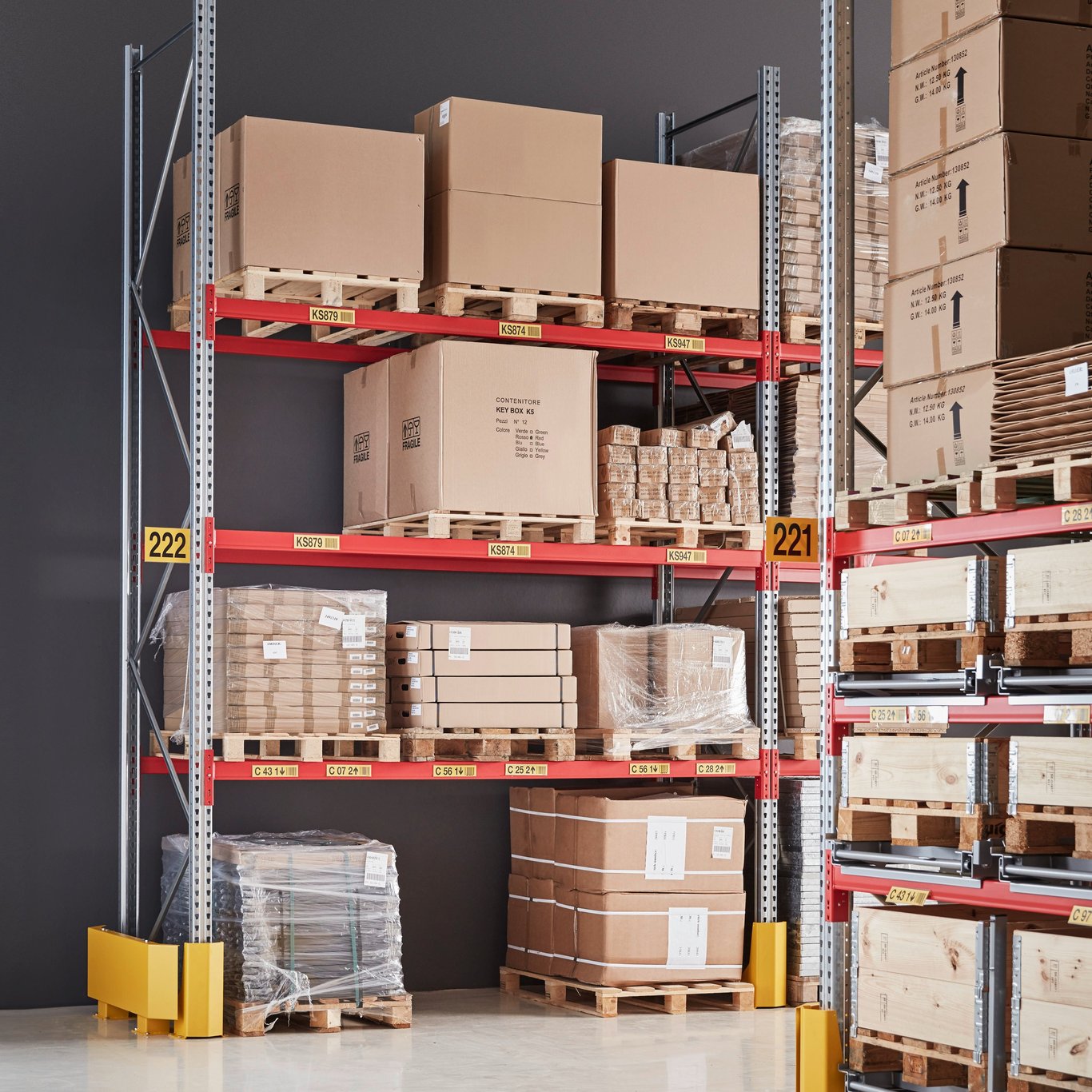
Remember to keep some space free
When will your warehouse be full? To facilitate efficient handling of incoming goods, an ideal fill rate of 80-85% is recommended for the warehouse. This allows for ample temporary storage space during delivery peaks. Consistently operating at a lower fill rate can lead to increased operational challenges and costs. In such cases, options include optimizing existing floor space, expanding storage capacity with additional shelves and pallet racks, or relocating to a larger facility.
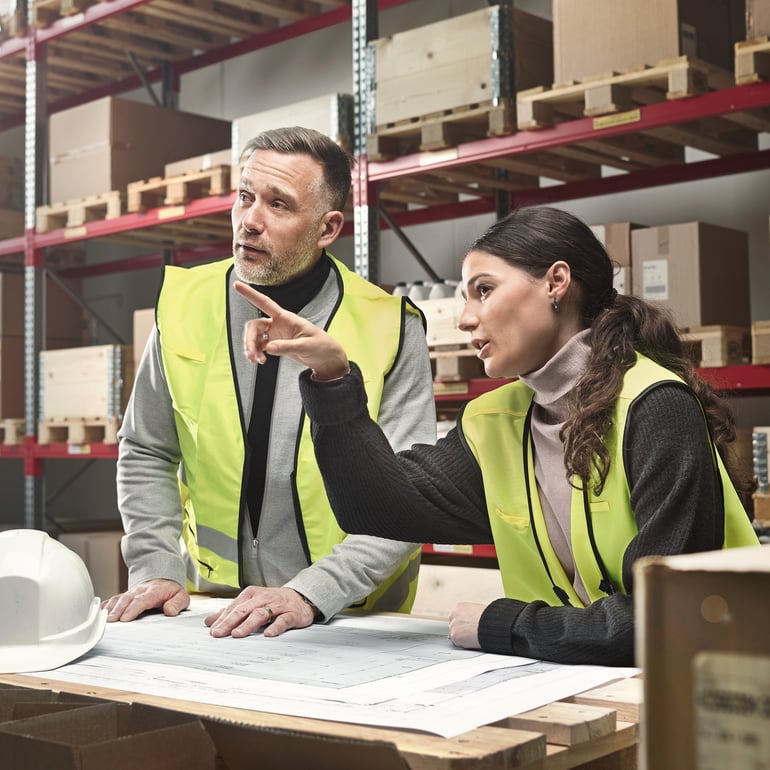
Storage system for goods
- Pallet Racks are racks made up of beams and are the most common type of storage for pallets in industrial warehouses.
- Free stacking means that pallets of goods are placed directly on the floor. More pallets are then stacked on top.
- Automated warehouses mean that cranes and transport lanes for pallets are automated. This solution is common on very large warehouses.
- Shelf compartments are used for smaller goods that are not loaded on a pallet. Shelf storage can also be automated.
Products for well-planned warehouses
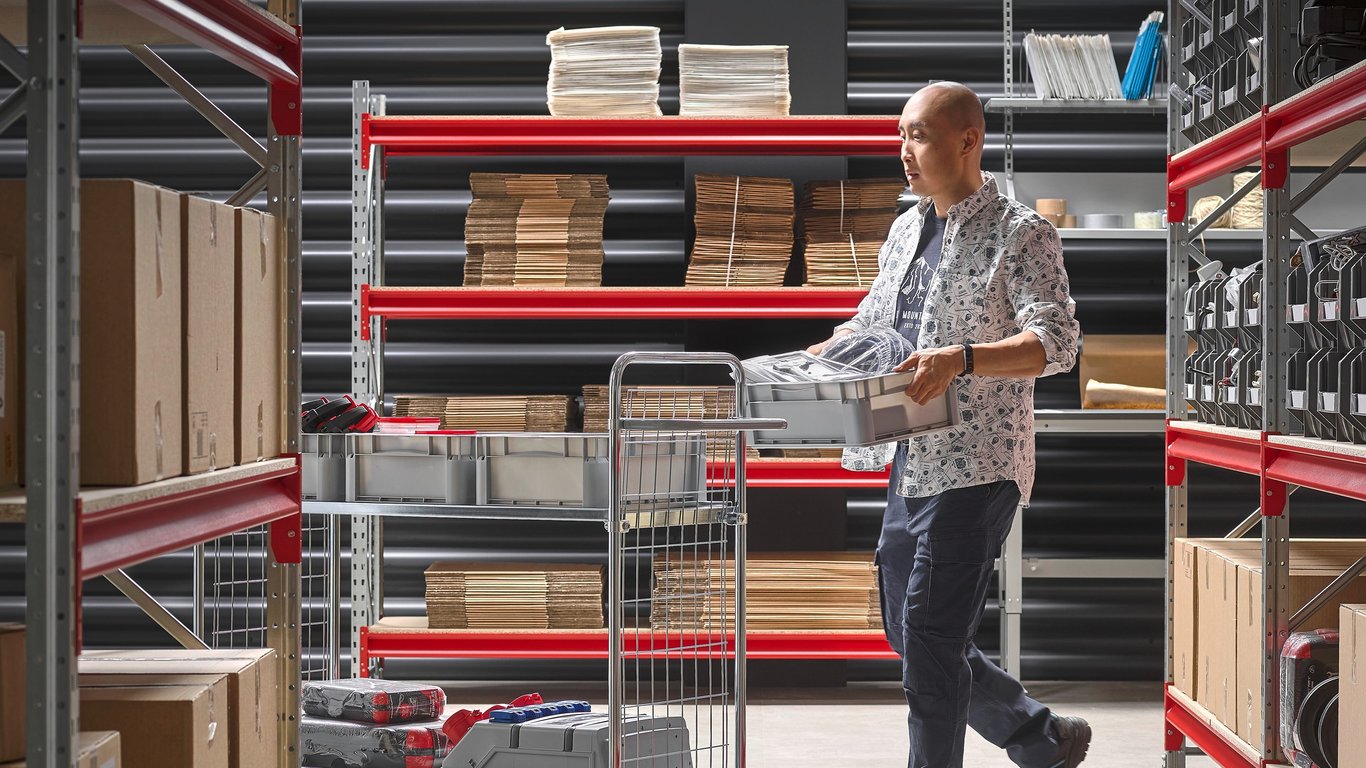
Update your fixtures and fittings regularly
Has the type of goods you work with changed? Is this change permanent? Then it's time to take action. You may need to make changes on an ongoing basis. The key to efficient warehouse management is to have fittings that are designed for the goods you store. If some of the goods you are stocking are small but are kept on shelves designed for other larger items, this means that you are storing a lot of fresh air, but the set up makes it impossible for you to increase your storage capacity. However, if you change the depth of the shelves to meet your new requirements, you can free up floor space for more shelving units and increase your capacity.
Another idea for getting more out of your warehouse is to take full advantage of the ceiling height and expand upwards. However, it's important to bear in mind that shelves that are very deep and very high make the products more difficult for your picking staff to reach. Fitting out your warehouse in the best way is a balancing act between maximising use of space and accessibility.
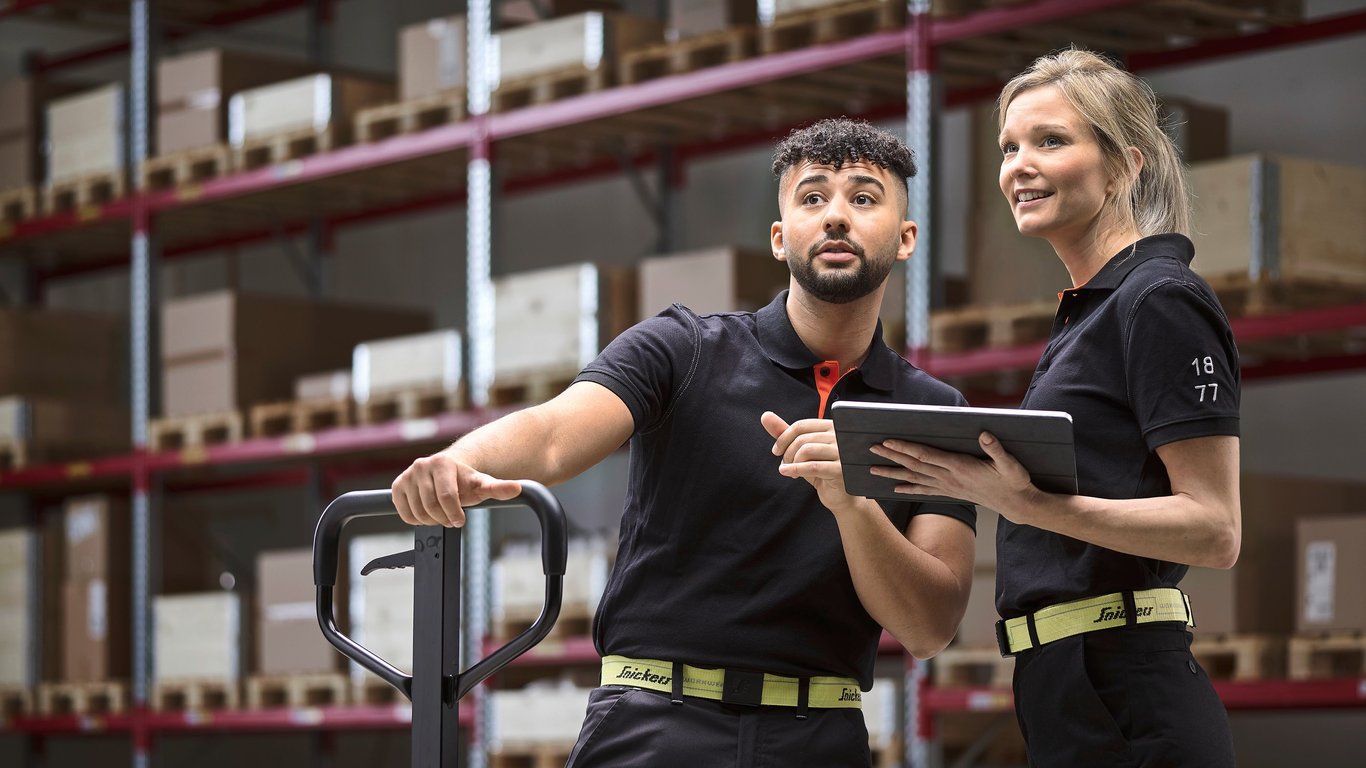
Optimise working conditions for warehouse staff
Has your customer service team received an increasing number of complaints about incorrect picking and damaged goods recently? Then it's time to take a look at the working conditions of your warehouse staff because unnecessarily long journeys and complex picking routines can cause a lot of problems. If it becomes more difficult for people to do their jobs because of circumstances outside their control, it can often lead to stress. This type of stress can easily result in mistakes being made, which customers will see as poor quality and careless service.
The well-being of your employees can affect your entire business. By giving them the right working conditions to do a good job, you are investing in both quality and efficiency.
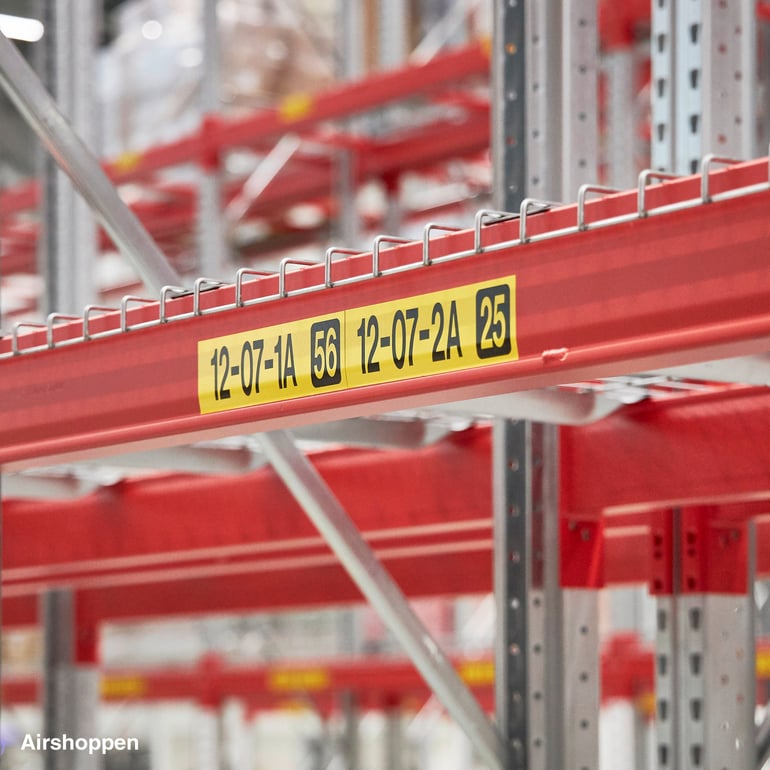
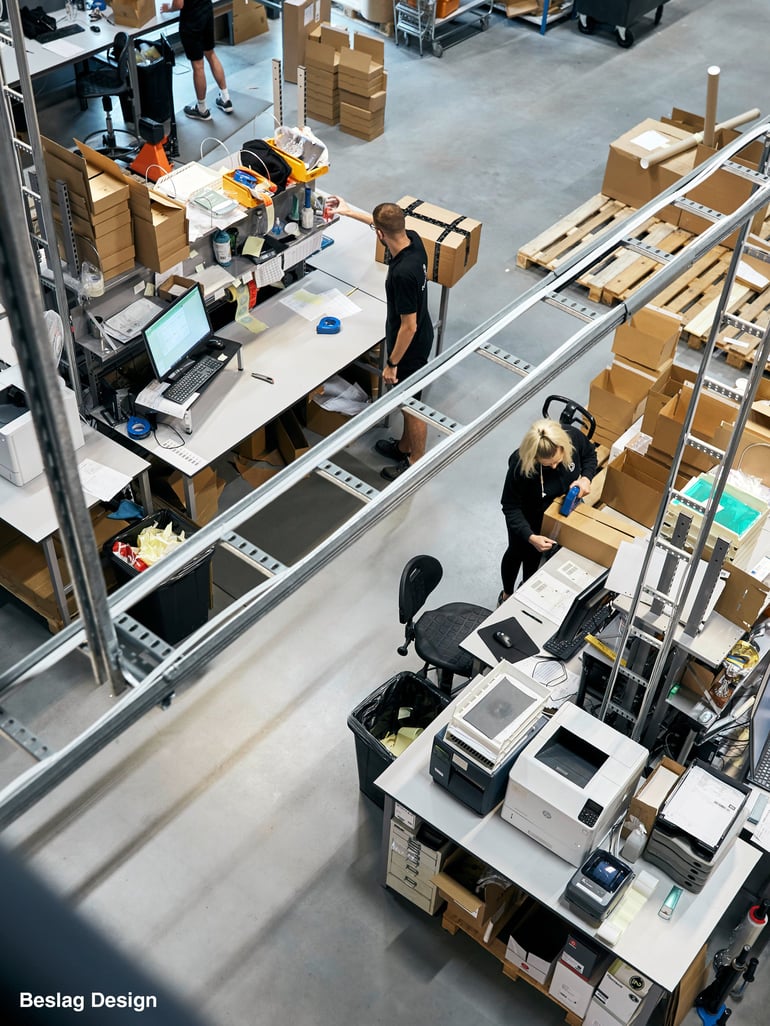
Products for well-planned warehouses
The right equipment
What can you do to make work in the warehouse easier? It's all about being organised and saving time. The top priority is for every product to have a designated place on the shelves that is clearly marked and easy to find. It's also important to have well-equipped packing tables nearby to make packing easier. Remember to have plenty of workstations so that no one has to wait and waste time unnecessarily.
Appropriate trolleys and lifting equipment perform two functions: they make the work more efficient and provide an ergonomic work environment that reduces the risk of injuries.
It's also a good idea to have recycling stations in strategic positions. This means that discarded materials are recycled straight away without wasting time. The result is no litter or blockages in the aisles.
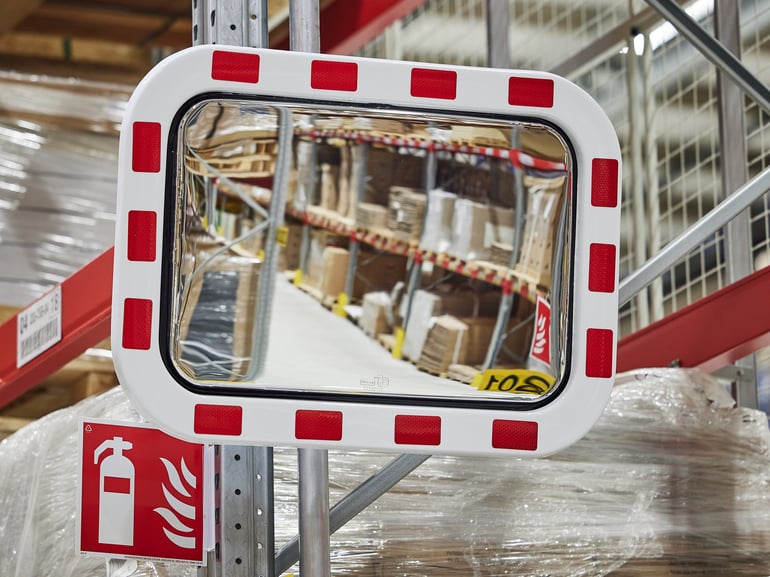
Increase security in the warehouse
Effective safety measures are essential for large and heavy pallet racks. It is crucial to select high-quality pallet racks that comply with industry safety standards. In the event of a potential accident involving a truck, there is a risk of instability. To safeguard the warehouse's pallet racks, various safety measures such as collision protection and gable protection are necessary. Additionally, the installation of anti-fall protection can prevent goods from falling behind the racks.
A comprehensive assessment, such as those covering machinery, storage facilities, and vehicle pathways, plays a pivotal role in enhancing safety standards. The installation of traffic mirrors in areas with limited visibility significantly improves warehouse safety. Strategic placement of monitoring mirrors is essential for accident prevention in dynamic warehouse environments. Adequate lighting is a must to ensure optimal visibility within the premises.
Here you can read more about safer warehouse and industrial environments.
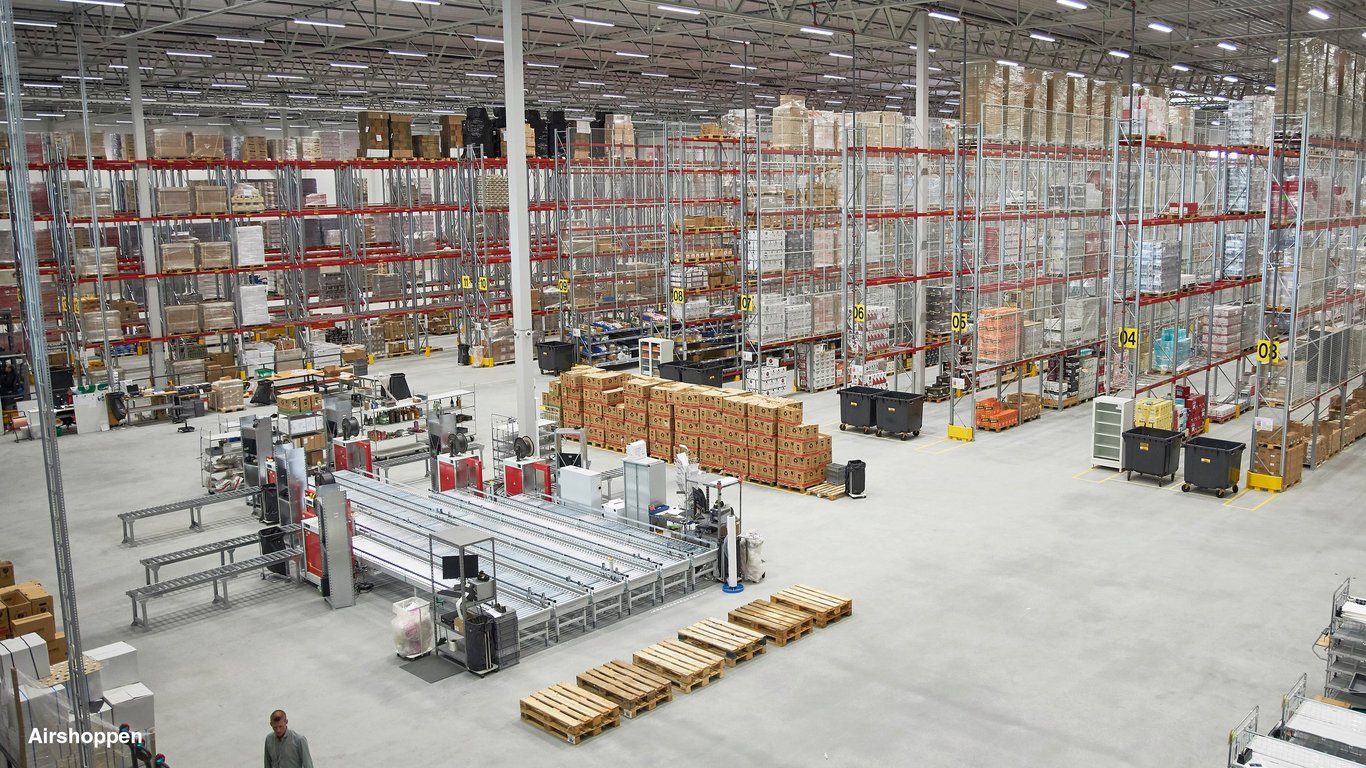
Give your customers what they want
Are you sometimes forced to turn down business because the warehouse can't keep up with demand? Are your delivery times sometimes so long that your customers give up and go to another supplier? Then it's time to take action, reverse the trend and create a warehouse that can provide the level of service that your customers expect.
Regardless of whether you want to resolve a problem or are wondering which warehouse products can best meet your needs, our warehouse experts are here to help. Our aim is to find the best warehouse solution for you. No job is too big or too small. Give us a call and take the first step towards a well-designed warehouse solution that will satisfy both your customers and your employees.
FAQ
Need help? Ask our interior experts!
We at AJ Products are always available to help you with solutions suited just for your business. Contact us if you have questions on the choice of fabric, need some inspiration or want to know the alternatives that would best suit your premises. We can then tell you more about your choices.Essentials for a well-managed warehouse
Get the latest product launches and offers sent direct to your inbox
Do you want to receive exclusive offers, information about new products and inspiration on how you can improve your workplace? Sign up for our free newsletter and be the first to receive our best offers.*By clicking subscribe, I confirm that I have read the privacy policy.